How a Chemical Defoamer Can Boost Efficiency in Your Workflow and Procedures
In today's affordable industrial landscape, operational efficiency is critical, and the function of a chemical defoamer can not be ignored. By dealing with foam-related challenges that interfere with procedures, defoamers not only promote smoother operations but additionally add to cost savings and enhanced item top quality.
Recognizing Chemical Defoamers
Chemical defoamers play a critical role in different industrial processes by effectively decreasing and avoiding foam development. Frothing can bring about functional inefficiencies, increased manufacturing expenses, and compromised item high quality. Defoamers are specialized chemical additives developed to interrupt the security of foam bubbles, thereby making it possible for smoother handling and improved efficiency across a number of fields, consisting of food and beverage, pharmaceuticals, and wastewater treatment.
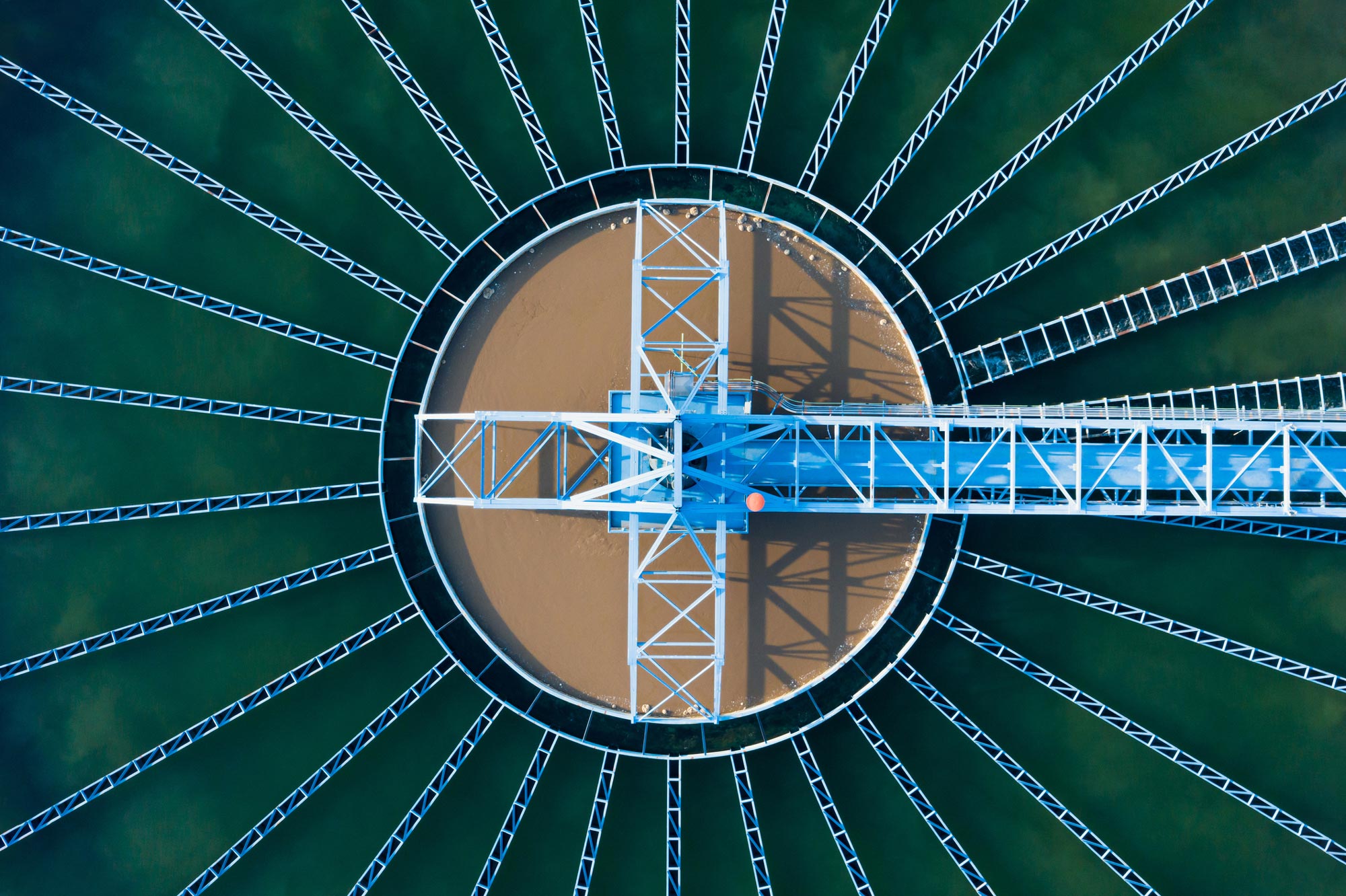
These representatives normally include surfactants, oils, or polymeric compounds that reduced the surface stress of the liquid, promoting the collapse of foam. The system through which defoamers operate often includes the destabilization of foam frameworks, enabling quicker drain of liquid and the launch of trapped air. Different solutions are tailored to details applications, thinking about variables such as compatibility with the system, temperature level, and the nature of the fluid being treated.
Recognizing the composition and performance of chemical defoamers is essential for choosing the proper item for a given application. By maximizing defoamer choice based upon process demands, sectors can enhance operational effectiveness, minimize foam-related challenges, and eventually improve general productivity.
Benefits of Using Defoamers
Using defoamers can dramatically boost functional performance across various markets by properly mitigating foam-related issues. The presence of foam can interrupt processes, resulting in boosted downtime, lowered productivity, and potential quality deterioration in output. Defoamers aid battle these obstacles by breaking down foam structures, thus permitting smoother operations.
One of the main benefits of utilizing defoamers is the reduction of waste and rework. By minimizing foam formation, defoamers enhance the uniformity of processes, guaranteeing that materials are used successfully. This not just decreases operational costs however also adds to sustainability initiatives by decreasing source consumption.
In addition, defoamers can boost item top quality. In producing settings, excessive foam can result in disparities in product characteristics, impacting customer satisfaction. By regulating foam degrees, defoamers assist maintain the preferred physical residential properties of items.

Applications in Various Industries
The performance of defoamers expands across a large range of sectors, where their application addresses specific foam-related difficulties intrinsic per field. In the food and beverage industry, defoamers are important for enhancing manufacturing processes, such look what i found as brewing and dairy processing, where extreme foam can impede circulation prices and minimize performance. By decreasing foam, these representatives boost item top quality and uniformity.
In the chemical production field, defoamers are employed in procedures like paint manufacturing and wastewater therapy. Below, they prevent foam formation that can interfere with mixing and different stages, thus boosting the general efficiency and effectiveness of operations.
In pharmaceuticals, defoamers play a vital role in the formulation of fluid drugs, guaranteeing correct dosage and stability by regulating foam throughout mixing and storage space. (Chemical Defoamer)
Additionally, in the farming industry, defoamers are made use of in pesticide solutions to improve application effectiveness and lessen waste.
Choosing the Right Defoamer
Choosing the appropriate defoamer is crucial for attaining optimum performance in various applications. The selection procedure ought to start with a thorough understanding of the particular More Info issues available, including the kind of foam existing, the processing conditions, and the chemical compatibility with various other formula elements.
Defoamers are developed from a selection of materials, consisting of silicone, mineral oils, and fats. Identifying the right structure is vital, as different products display differing efficiency in diverse settings. Silicone-based defoamers are commonly favored in high-temperature applications due to their stability, while natural defoamers might be more appropriate for water-based systems.
Additionally, take into consideration the defoamer's influence on the end product. Some solutions can alter the practical or aesthetic buildings, making it necessary to select a defoamer that satisfies product specs without endangering quality.
Examining is another crucial action in selecting a defoamer. Small-scale tests can provide useful understandings into the defoamer's efficiency, enabling adjustments prior to full-scale application. By carefully assessing these variables, businesses can improve performance and ensure that the defoamer efficiently fulfills their functional requirements.
Ideal Practices for Implementation
Executing a defoamer properly calls for mindful planning and adherence to ideal techniques to optimize its efficiency. First, carry out a thorough analysis of the specific application and foam qualities. Recognizing the kind and resource of foam will certainly guide the selection of one of the most appropriate defoamer formulation.
Following, establish the optimum dose (Chemical Defoamer). Start with a small test to determine the minimal reliable focus, as too much usage can bring about damaging effects on product quality or operational efficiency
Monitoring and readjusting the application approach is crucial; ensure that the defoamer is presented at the appropriate point in the process for maximum influence, such as during blending or immediately after foam development.

Furthermore, keep clear communication with all pertinent workers to make certain consistent application methods and to share understandings on efficiency results.
Conclusion
To conclude, the usage of chemical defoamers plays an essential duty in improving functional efficiency across varied sectors. By effectively destabilizing foam, these agents help with quicker water drainage and air launch, thereby reducing disturbances and lowering expenses. The calculated application of defoamers not just enhances throughput yet likewise guarantees regular product quality and view source optimization. Ultimately, the unification of defoamers into industrial procedures fosters dependability and adds to total performance improvement.

In the food and beverage market, defoamers are crucial for optimizing manufacturing procedures, such as brewing and milk handling, where extreme foam can impede circulation prices and lower performance. Silicone-based defoamers are usually favored in high-temperature applications due to their stability, while natural defoamers might be a lot more appropriate for water-based systems.